Blog
Our Product & Service
Menu
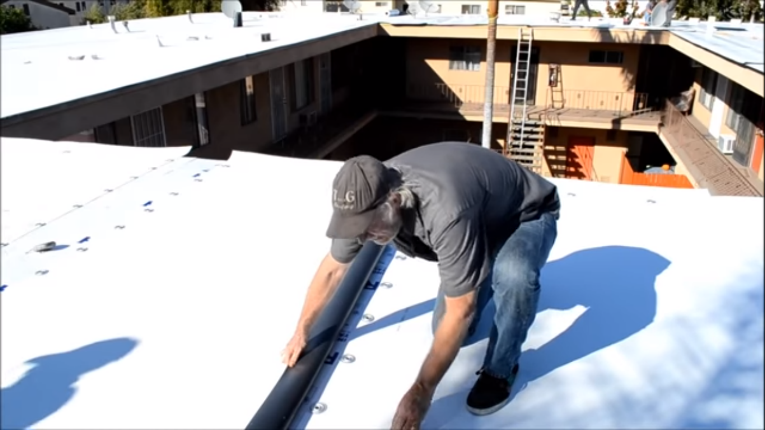
Figure 1: Thermoplastic Membrane
Thermoplastic membrane is made of polymers such as polyvinyl chloride (PVC), chlorinated polyurethane, or chlorosulfonated polyethylene. The glass-reinforced PVC is the most popular type of thermoplastic membrane. It has a typical lifespan of 22 to 30 years.
The thermoplastic membrane has many advantages. For example, it possesses elongation properties and high resistance to chemical and hydrostatic pressure. It can also be applied at seams with ease with solvent-based adhesives or with the aid of heat-welding. It can also be cropped to accommodate application in places with irregular shapes. Figure 2 shows the thermoplastic membrane is cropped to cover a column. However, it also comes with some shortcomings. When it is subjected to high temperatures, its strength will be highly affected. Besides, it will be degraded when it comes in contact with hydrocarbon materials, like asphalt, fuel, and lubricant oil.
Application of the thermoplastic membrane requires the contact surface reasonably free from defects like a floor with a steel trowel finish to ensure good adhesion. It is usually not suitable to be implemented on the rooftops due to the hot weather. Hence, it is more suitable to be applied in cool places, such as tunnel structures and underground structures. Its good chemical and hydrostatic pressure resistance also allow it to be applied at ponds, swimming pools, and water tanks.
A thermoplastic membrane can be used to tackle water leakage issues. It has elongation properties, high chemical resistance, and high hydrostatic pressure resistance, but it will be weakened in high temperatures. Hence, it is suitable to be applied in cooler places, such as tunnels and water tanks. In this way, its strengths are fully utilized, and its weaknesses are effectively minimized.